Попробуйте вообразить, что в один далеко не прекрасный день на Земле вдруг исчезли бы все болты, винты, гайки и шайбы. Произошла бы величайшая катастрофа. Все начало бы рушиться. Ведь в любой машине, от карманного фонарика до атомного ледокола, обязательно работают малозаметные, но очень нужные, всем нам хорошо знакомые детали, именуемые крепежом. Да, машина без крепежа — это одежда без пуговиц.
Вероятно, многим из вас в свое время дарили замечательную игру — конструктор. Вспомните, с каким увлечением вы сооружали различные механизмы и модели, старательно закручивая винты и гайки. А не будь в комплекте этих необходимых мелочей, у вас бы ничего и не вышло. И это не только в игре. У каждого уважающего себя механика всегда под рукой ящичек или баночка с набором винтов, болтов, гаек и шайб, тщательно разобранных по размерам.
Основой рассматриваемых нами соединительных деталей является винтовая нарезка, или, проще — резьба, одно из гениальнейших изобретений человека. Идея практического применения винта родилась очень давно. Вспомните хотя бы Архимедов винт. Но вот минули тысячелетия, а таких элементарных деталей, как винт и гайка в нашем сегодняшнем представлении, люди не имели даже в начале прошлого века.
На металлообрабатывающих предприятиях и в старину, конечно, существовали способы изготовления резьбовых деталей, но, как вы сейчас увидите, весьма далекие от совершенства.
Круглую металлическую заготовку обматывали двумя проволоками, под требуемым углом плотно прижимая витки друг к другу. Затем одну проволоку аккуратно удаляли и получали винтовую канавку, соответствующую виткам будущей резьбы. Заготовку с оставшейся на ней проволокой погружали в расплавленное олово и таким образом спаивали. Залитое оловом пространство между витками давало направление резцу, с помощью которого ударами молотка выполняли нарезку, а завершали эту операцию тщательной опиловкой. Гайка изготавливалась тоже весьма примитивно и подгонялась к болту индивидуально. Естественно, что при такой «технологии» изготовления трудно было найти два одинаковых болта или гайки. Перепутав эти пары, рабочий уже не мог ими пользоваться, так как подобрать из кучки деталей гайку к болту было практически невозможно.
Но вот в начале XVIII века русский механик Андрей Мартов и спустя несколько десятилетий английский инженер Генри Моделей создали токарно-винторезный станок с самоходным суппортом, что позволило механизировать операции по нарезанию резьбы. Изобретение быстро завоевало широкое признание промышленных кругов. Позже Моделей сделал еще один весьма важный шаг: он упорядочил резьбовое хозяйство. Ведь в те времена каждый разработчик был волен творить для своих деталей диаметр, шаг резьбы и ее профиль по собственному усмотрению, не сообразуясь с аналогичными работами коллег на других предприятиях, а тем более в других городах и странах. Моделей понимал, что возникла острая необходимость стандартизации, обеспечивающей взаимозаменяемость крепежа. Эту огромную работу продолжил воспитанник Моделея — Витворт. Только в середине XIX столетия в Англии впервые утвердилась стандартная резьба — резьба Витворта, которая постепенно начала внедряться и в ряде других стран, в том числе и в России.
Все же единого международного стандарта на резьбы, к сожалению, нет и по сей день. Даже такие промышленно развитые страны, как Англия и США, еще не перешли на общепринятую метрическую систему мер и применяют в своих разработках резьбу дюймовую.
В нашей стране метрическая система мер введена в 1918 году как наиболее удобная и прогрессивная, и вместо дюймовой стала применяться резьба метрическая. Поэтому какой-нибудь винт от старого велосипеда, предусмотрительно сбереженный вами, со временем может пригодиться при ремонте, например, электрополотера, пылесоса, да мало ли для чего еще... А вот от английского магнитофона ни один винтик, ни одна гаечка не подойдет ни к нашим, ни к немецким, ни к другим европейским изделиям.
Промышленность может нам сегодня предложить великое многообразие крепежа. На первый взгляд это кажется странным. Может возникнуть вопрос: почему нельзя повсеместно применять, например, самый обычный болт с шестигранной головкой и варьировать только его размеры? Попробуем немного пофантазировать (очень полезное занятие для конструктора): увидим в каком-нибудь устройстве винт и мысленно заменим его болтом. Интересно, что у нас получится?
А как будет выглядеть механизм наручных часов, у которых вместо аккуратных потайных головок микроскопических винтиков вылезли, как грибы, шестигранные головки болтов? Такое безобразие и представить трудно.
Но если нам доведется принять участие в разборке магнитофона, то в его механизмах уже могут встретиться и болты. Посмотрите на велосипед — добрую половину крепежа составляют болты и гайки, а в конструкции трактора их еще больше, да и в механизме часов, но уже башенных, болты уже весьма солидных размеров будут тоже не редкостью.
Напрашивается вывод: для соединения деталей, несущих большую нагрузку, применяются болты, а там, где больших нагрузок нет, предпочтение отдается винтам.
Затяжка болтов и гаек обычно производится гаечными ключами, с помощью которых можно создать огромный крутящий момент. Например, мы орудуем ключом длиною 20—30 см, нажимаем на него с силой 10—15 кг и получаем момент в сотни кг/см. Резьба, как известно, представляет собой разновидность пологой наклонной плоскости, следовательно, этот момент разовьет осевое усилие, сжимающее сопрягаемые детали, в тысячи килограммов.
Ну вот, некоторое различие в способе установки крупного и мелкого крепежа мы уяснили. Теперь попытаемся разобраться в многообразии ассортимента крепежа. Ведь единообразна только резьбовая часть, а стержень и головка имеют множество модификаций (видоизменений), что определяется главным образом конструктивными и технологическими требованиями. Конечно, представить всю номенклатуру (перечень названий) крепежа невозможно, поэтому рассмотрим только самый ходовой товар:
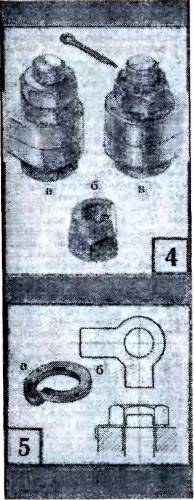
— Винт с потайной головкой (рис. 1а) очень удобен тем, что полностью вписывается в габарит контактируемых деталей, но его головка имеет сравнительно большой диаметр и мелкий шлиц (прорезь под отвертку). Если в процессе эксплуатации винт потребуется часто отворачивать и вновь заворачивать, шлиц быстро помнется (чаще говорят, сорвется), что не обеспечит плотной затяжки винта, и его придется заменить новым.
В последнее время широкое распространение получили крестообразные шлицы (рис. 1б), они хороши тем, что конусообразный конец специальной отвертки как бы сам находит шлиц, что существенно облегчает завертывание и отвертывание винтов, особенно при плохом освещении.
— Винт с полупотайной головкой (рис. 1в) имеет более глубокий, а следовательно, и более крепкий шлиц, но выступает за габариты закрепляемой детали, что не всегда допустимо по конструктивным соображениям.
— Винт с полукруглой головкой (рис. 1г). Здесь вся головка выступает над поверхностью закрепляемой детали, но диаметр головки на 15—20% меньше, чем потайной, что в случае стесненных габаритов весьма полезно.
— Винт с цилиндрической головкой (рис. 2а) имеет наименьший диаметр головки, глубокий и более прочный шлиц. Иногда выполняется внутренний шестигранный шлиц, который выручает нас тогда, когда для отвертки нет доступа сверху. В этом случае конструктор предусматривает над посадочным отверстием для винта некоторое свободное пространство, чтобы иметь возможность поставить винт и подойти специальным ключом (рис. 2б).
Кроме того, плоская, а не коническая форма основания головок (полукруглой и цилиндрической) дает возможность подкладывать под нее пружинную шайбу (рис. 5а) и тем самым обеспечивать контровку.
— Болт с квадратной головкой (рис. За) очень удобен в конструкциях, где в малых габаритах требуется создать плотное соединение деталей. Диаметр его головки на 35—40% меньше шестигранной.
— Конусный болт (рис. 3б) очень хорош для обеспечения безлюфтового соединения деталей — например, для крепления педальных рычагов на оси каретки велосипеда.
— Откидной болт (рис. Зв) чаще всего применяется для различного рода прижимных устройств, которыми регулярно пользуются в процессе эксплуатации, — например, для герметизации крышек баков.
Теперь коротко о гайках. Эта простейшая деталь совместно с болтом обеспечивает крепкое соединение деталей, что, как известно, достигается без особого труда. Значительно сложнее добиться, чтобы гайка в процессе работы не отворачивалась, даже если ей приходится испытывать вибрационные перегрузки, возникающие при работе в конструкциях, например, самолетов, автомобилей, станков и многих других машин. Здесь приходится прибегать к «маленьким хитростям».
Вот несколько простейших способов контровки, наиболее часто встречающихся в практике машиностроения:
— За основной гайкой наворачивается и плотно затягивается еще одна, так называемая контргайка (рис. 4а), что значительно повышает устойчивость системы против самоотворачивания.
— Самоконтрящаяся гайка (рис. 4б). Над резьбой в корпусе гайки наглухо завальцовывается фибровое колечко, внутренний диаметр которого несколько меньше наружного диаметра резьбы болта. При наворачивании гайки фибра плотно вдавливается в резьбу и благодаря большому давлению и высокому коэффициенту трения удерживается от непроизвольного отворачивания.
Но фибра не резина, и при повторном заворачивании плотного сцепления с резьбой уже не получается. Поэтому в ответственных соединениях такие гайки используют один раз.
— Корончатая гайка (рис. 4в) в верхней части имеет радиальные прорези. При затяжке гайки одну из прорезей совмещают с отверстием в резьбовой части болта и вставляют шплинт. Этот вид контровки надежнее предшествующих, и все же бывали случаи, правда, очень редкие, когда под воздействием внешних сил шплинт срезался и контровка нарушалась. Шплинтовать гайку с диаметром резьбы менее 5 мм не рекомендуется.
— Очень распространена контровка с помощью пружинной шайбы (рис. 5а), которая выполнена в виде витка пружины прямоугольного сечения с заостренными концами, срезанными под углом 75°. При затяжке шайба сжимается и острыми кончиками как бы впивается в материал, удерживая крепеж в зажатом состоянии. Этот вид контровки особенно удобен для крепежа малого диаметра.
— Иногда болты и гайки контрят стопорными шайбами с лапками (рис. 5в).
Не подумайте, что шайбы применяются только для стопорения. Наибольшее распространение имеют самые простые круглые шайбы, которые подкладывают под головку болта (винта) или под гайку для защиты поверхности детали. В деревянных конструкциях шайбы с большим наружным диаметром рекомендуется подкладывать и под гайку и под головку болта для увеличения опорной поверхности с целью уменьшения удельного давления на дерево.
Остряки говорят: «Не изобретайте велосипед», то есть не растрачивайте время на разработку конструкций, которые давно нашли широкое применение и в течение многих лет непрестанно совершенствовались. Настоящий конструктор с этим никогда не согласится, так как в технике нет и не может быть абсолютного совершенства. И новые велосипеды все-таки изобретают, и не без успеха. Для нашего сегодняшнего разговора любопытно отметить, что в официальном бюллетене Государственного комитета Совета Министров СССР по делам изобретений и открытий среди множества технических новинок самого различного направления почти каждую неделю публиковались авторские свидетельства на изобретение новых болтовых соединений, гаек, шайб и других крепежных устройств.
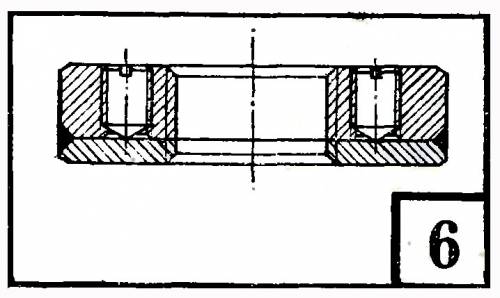
Обратите внимание на рисунок 6. Изобретателю Н. Бычкову (авторское свидетельство № 619699) в габаритах обычной гайки удалось получить новое качество — обеспечить ее стопорение благодаря дополнительному давлению на поверхность резьбы с помощью нажимных винтов.
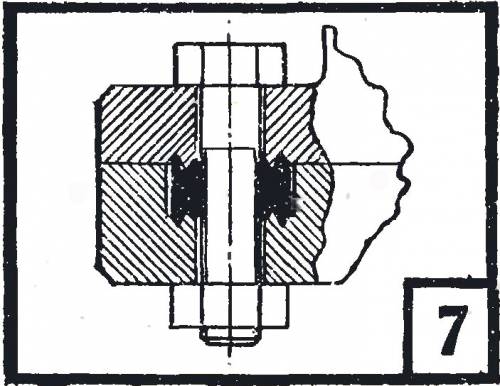
А на рисунке 7 изображено болтовое соединение (авторское свидетельство № 621904), которое разрабатывали изобретатели А. Малицкий и Ю. Иванов. Между контактирующими поверхностями оно содержит фиксирующий элемент с острыми микровыступами. Внешне он похож на гайку и размещается в углублениях обеих деталей. Фиксирующий элемент повышает устойчивость к сдвигу. |